Quick and Reliable Product Packaging Maker Repair Service Services to Minimize Downtime
In the affordable landscape of manufacturing, the efficiency of product packaging operations depends upon the integrity of machinery. Quick and dependable repair solutions are crucial in reducing downtime, which can bring about considerable financial losses and functional problems. Comprehending the importance of prompt interventions and the function of expert service technicians can transform just how companies come close to maintenance and repair services. Navigating the myriad choices readily available for repair work solutions can be challenging. What aspects should organizations think about to guarantee they are making the right option for their functional demands?
Importance of Timely Repairs
Timely repair work of packaging devices are important for preserving operational efficiency and reducing downtime. In the fast-paced environment of production and packaging, also small malfunctions can cause considerable hold-ups and efficiency losses. Dealing with issues quickly ensures that machines run at their optimum capability, thus protecting the flow of procedures.
Moreover, normal and timely maintenance can prevent the escalation of small issues into significant failures, which commonly incur higher fixing expenses and longer downtimes. A proactive approach to equipment repair work not only maintains the stability of the equipment yet likewise enhances the total reliability of the assembly line.
Furthermore, timely fixings contribute to the long life of packaging equipment. Makers that are serviced quickly are much less likely to deal with extreme damage, enabling businesses to optimize their investments. This is particularly important in sectors where high-speed product packaging is essential, as the demand for consistent efficiency is paramount.
Benefits of Reliable Solution Suppliers
Dependable service companies play an essential function in making sure the smooth procedure of product packaging equipments. Their expertise not only enhances the efficiency of repairs but also contributes significantly to the longevity of tools.
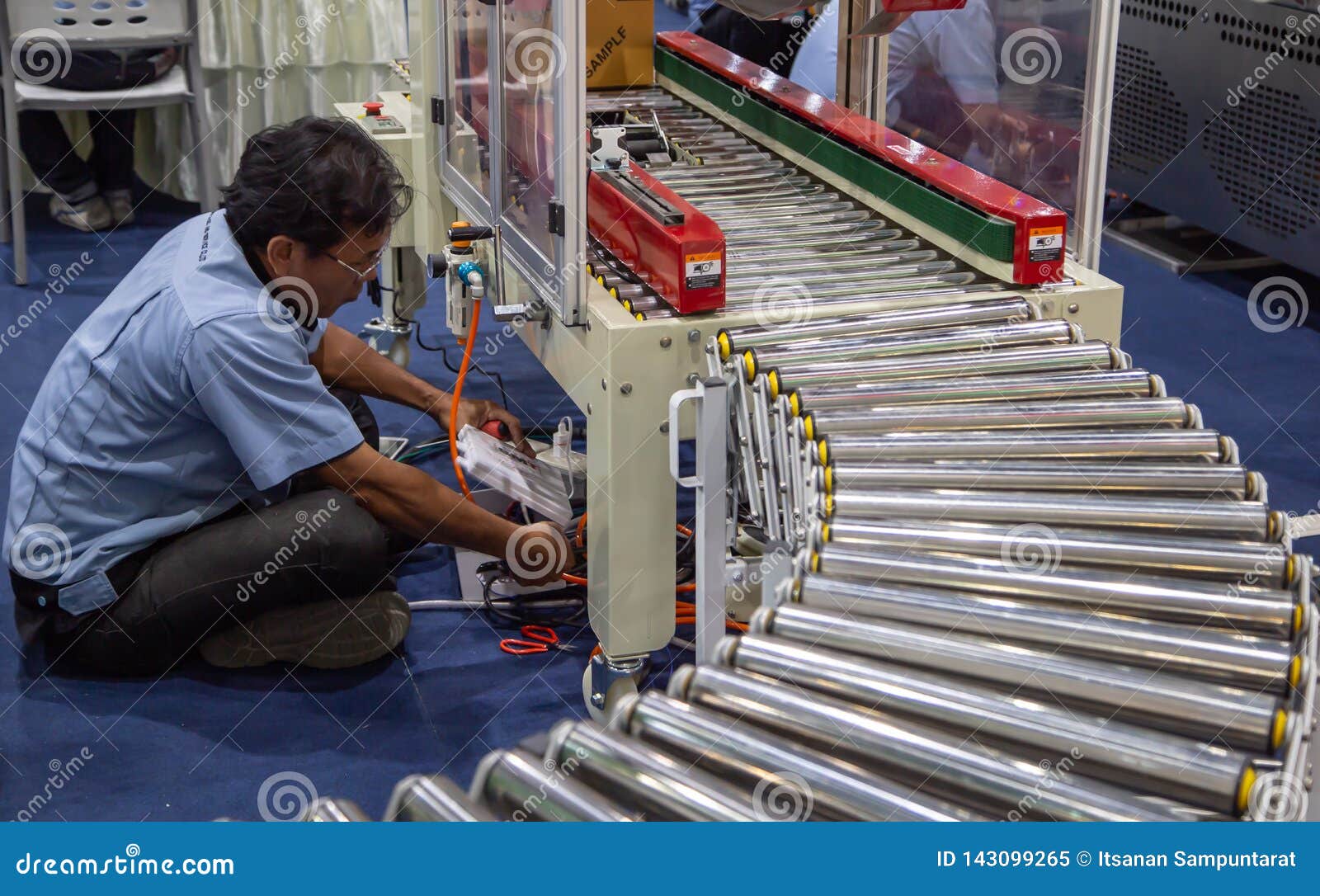
In addition, a trustworthy company offers comprehensive support, consisting of training and advice for team on equipment procedure and upkeep finest methods. This not only equips employees but also grows a society of safety and security and effectiveness within the organization. In general, the benefits of involving trusted solution suppliers prolong beyond immediate repairs, favorably affecting the entire operational operations of product packaging processes.
Common Product Packaging Maker Problems
In the realm of product packaging procedures, various issues can jeopardize the effectiveness and performance of machines. One widespread issue is mechanical failure, often originating from deterioration or inadequate upkeep. Parts such as belts, motors, and equipments may fall short, causing breakdowns that stop production. An additional common concern is misalignment, which can create jams and unequal product packaging, affecting item quality and throughput.
Electrical issues can additionally disrupt product packaging operations. Malfunctioning wiring or malfunctioning sensors might result in unpredictable equipment behavior, read the full info here triggering hold-ups and raised operational expenses. In addition, software glitches can impede the equipment's programming, resulting in functional inadequacies.
Inconsistent product flow is one more essential issue. This can occur from variations in item shape, weight, or dimension, which might influence the equipment's capacity to handle items precisely. Lastly, inadequate training of drivers can worsen these troubles, as inexperienced employees might not identify very early indicators of breakdown or might abuse the tools.
Resolving these usual product packaging maker problems immediately is important to preserving efficiency and guaranteeing a smooth operation. Normal evaluations and proactive upkeep can dramatically minimize these problems, promoting a trustworthy product packaging atmosphere.
Tips for Minimizing Downtime
To minimize downtime in product packaging operations, executing an aggressive upkeep technique is essential. Routinely set up upkeep checks can identify possible problems before they rise, making sure devices run effectively. Establishing a regimen that includes lubrication, calibration, and examination of vital components can dramatically decrease the regularity of unforeseen breakdowns.
Educating staff to operate equipment properly and identify early indication of breakdown can also play an essential role. Encouraging operators with the understanding to perform fundamental troubleshooting can prevent minor concerns from causing significant hold-ups. Furthermore, keeping a well-organized stock of essential spare components can expedite repair work, as awaiting parts can result in extensive downtime.
In addition, documenting device efficiency and upkeep tasks can help identify patterns and frequent troubles, allowing for targeted interventions. Integrating sophisticated surveillance technologies can provide real-time data, allowing anticipating upkeep and lessening the threat of abrupt failings.
Lastly, fostering open communication between operators and maintenance teams ensures that any irregularities are quickly reported and attended to. By taking these positive procedures, services can improve functional effectiveness and substantially minimize read this article downtime in packaging processes.
Choosing the Right Repair Solution
Picking the appropriate repair service for product packaging equipments is a crucial decision that can significantly influence functional effectiveness. A well-chosen service provider makes certain that your equipment is repaired swiftly, effectively, and to the highest possible criteria. Begin by examining the supplier's experience with your certain sort of product packaging tools. A service technician familiar with your equipment can identify issues more properly and carry out services more swiftly.
Next, think about the service supplier's reputation. Looking for feedback from other organizations within your market can give insights right into reliability and high quality. Qualifications try here and partnerships with identified equipment makers can additionally indicate a dedication to quality.
Additionally, analyze their reaction time and schedule. A company that can supply prompt support decreases downtime and keeps production flow constant. It's also important to make inquiries about warranty and service assurances, which can mirror the confidence the service provider has in their work.
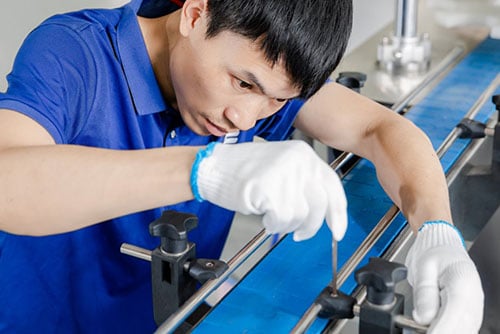
Conclusion
In final thought, the value of quick and trustworthy packaging equipment repair services can not be overstated, as they play a critical role in reducing downtime and making sure functional performance. Implementing positive maintenance methods and spending in team training more enhances the longevity of packaging machinery.
Timely repair work of packaging makers are critical for keeping functional performance and minimizing downtime.Additionally, timely repairs contribute to the longevity of packaging equipment. Overall, the advantages of involving trusted solution carriers expand past instant repair services, favorably affecting the entire functional process of packaging processes.
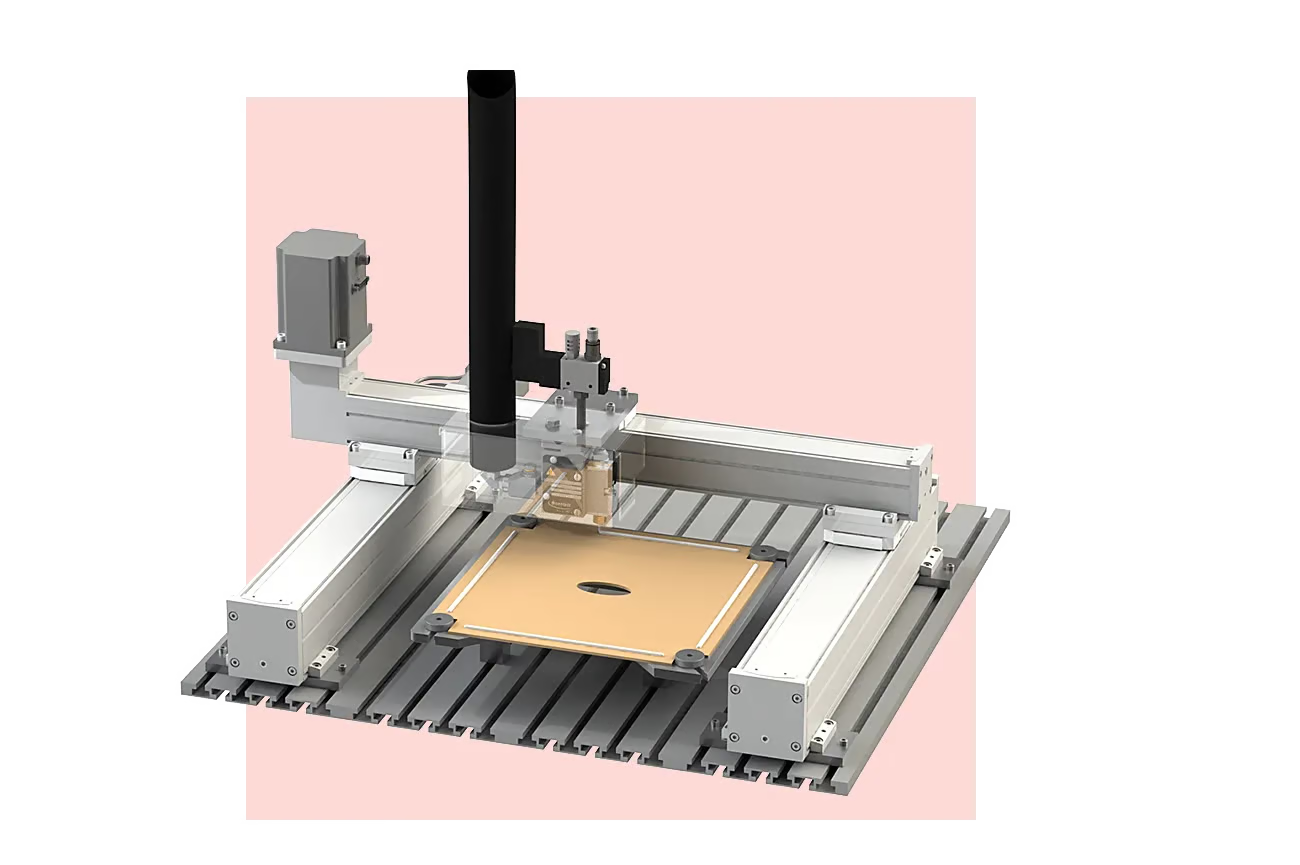